Aerospace
3D-printing solutions for the aerospace industry
The Aerospace and Defense (A&D) industry is a great example of utilization Additive Manufacturing (AM) (commonly referred to as 3D Printing) with a clear value proposition and the ability to create parts that are stronger and lighter than parts made using traditional manufacturing.
The A&D industry was a very early adopter of 3D printing and still continues to contribute heavily to its development. Some aerospace companies began using this technology as early as 1989 and over the next couple of decades, the adoption of 3D printing increased substantially. In 2015, the Aerospace & Defense industries contributed approximately 16% of 3D Printing’s \$4.9+ billion global revenues.
In the aerospace industry, the stakes are high. Manufacturers tasked with designing and building the type of high-precision, safety-critical parts required in such a highly regulated sector have no margin for error.
Engineers have come to rely on 3D-printing technology to get their ideas moving more quickly. When a business can produce bespoke models in-house and on-demand, testing is much faster and production efficiency is maximised, reducing product-to-market time and saving money.
It’s now possible to create lightweight, flight-ready aircraft parts in high-performance thermoplastics that offer the necessary temperature, chemical, UV and environmental resistance.
Why use 3D printing for aerospace design?
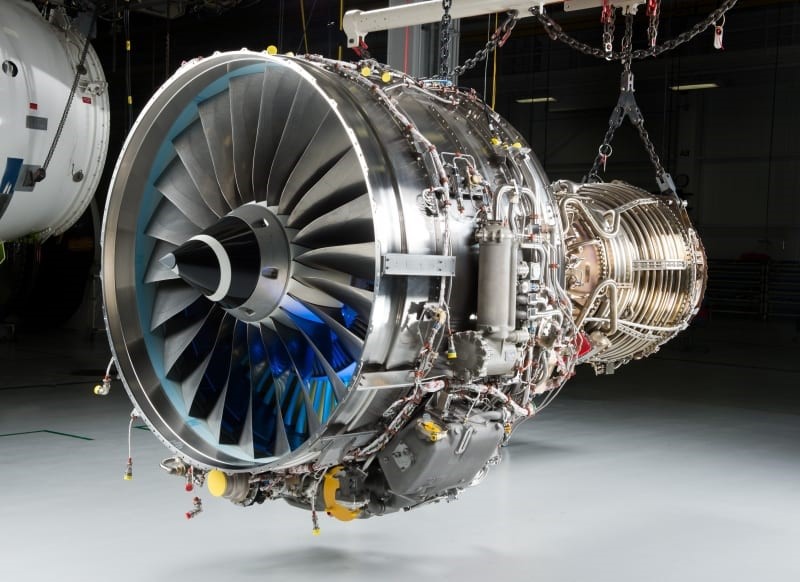
- Replace high-value, low-volume CNC-milled parts to dramatically speed up production and reduce costs
- Identify design issues more quickly by producing realistic prototypes for functional testing, before committing to expensive and time-consuming production
- Produce fixtures and lightweight, flight-worthy parts (eg housings and ductwork) in a fraction of the time it takes using traditional manufacturing methods
- Avoid high machining costs for custom tools or parts needed for maintenance by creating jigs and fixtures quickly and affordably
- Industrial 3D printing can manufacture very strong and lightweight structures that achieve weight reductions of around 40-60 %. The effects: leaner cost structures, material savings and lower fuel consumption.
- The tool-free production process allows product adaptations to be implemented more quickly. Spare part storage can be significantly reduced by manufacturing on demand without an extended lead time. The cost advantages become strongly apparent over the long life cycles of aircraft.
- Industrial 3D printing enables a wide range of design optimizations – from part customization and upgrades to exclusive innovations that can only be manufactured additively.
- Additive manufacturing is a tool-free process. This means that significant cost savings can be achieved in comparison to conventional manufacturing processes.