Automotive
Industrial-size 3D printers have opened up new opportunities for the automotive industry.
For the automotive industry recent advances in Additive Manufacturing (AM) (or 3D Printing) have opened doors for newer, more robust designs; lighter, stronger, and safer products; reduced lead times; and reduced costs. In 2015, the annual Wohlers report stated that the automotive industry accounted for 16.1% of all AM expenditure. While automotive original equipment manufacturers (OEMs) and suppliers primarily use AM for rapid prototyping, the technical trajectory of AM makes a strong case for its use in product innovation and direct manufacturing in the future.In a crowded automotive marketplace, knowing how to gain the edge over the competition is critical to ensuring prosperity – and that’s why the world’s most renowned companies in this sector have turned to 3D printing.
Automotive manufacturing requirements
Weight - final parts
One of the most critical aspects relating to the automotive industry is the weight reduction of components. Automotive applications make use of advanced engineering materials and complex geometries in an attempt to reduce weight and improve performance. AM is capable of producing parts from many of the lightweight polymers and metals that are common in the automotive industry.
Complex geometries - prototypes and final parts
Affecting weight and aerodynamics (and therefore vehicle performance) is the geometry of a part. Automotive parts often require internal channels for conformal cooling, hidden features, thin walls, fine meshes and complex curved surfaces. AM allows for the manufacture of highly complex structures which can still be extremely light and stable. It provides a high degree of design freedom, the optimization, and integration of functional features, the manufacture of small batch sizes at reasonable unit costs and a high degree of product customization even in serial production.
Temperature - testing and final parts
Many automotive applications require significant heat deflection minimums. There are several AM processes that offer materials that withstand temperatures well above the average sustained engine compartment temperatures.
Moisture - testing and final parts
Most components that go into the production of automobiles must be moisture resistant, if not moisture proof, entirely. One major benefit of additive manufacturing is that all printed parts can be post-processed in order to create a watertight and moisture resistant barrier. Additionally, many materials, by their very nature, are suited for humidity and moisture plagued environments.
Part consolidation - prototyping and final parts
The number of items in an assembly can be reduced by redesigning as a single complex component. Part consolidation is a significant factor when considering how AM can benefit the reduction of material usage, thereby reducing weight and in the long run, cost. Part consolidation also reduces inventory and means that assemblies can be replaced with a single part should repairs or maintenance need to take place; another important consideration for the automotive industry.

Part consolidation - prototyping and final parts
The number of items in an assembly can be reduced by redesigning as a single complex component. Part consolidation is a significant factor when considering how AM can benefit the reduction of material usage, thereby reducing weight and in the long run, cost. Part consolidation also reduces inventory and means that assemblies can be replaced with a single part should repairs or maintenance need to take place; another important consideration for the automotive industry.
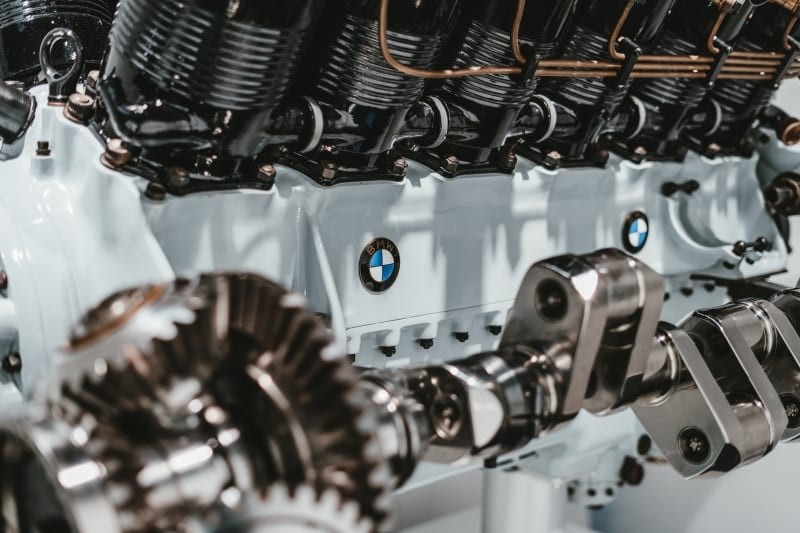
Why use 3D printing for automotive design?
- Prototype, test and produce all manner of tools, jigs, fixtures and car-ready parts with unprecedented speed
- Avoid scrap and retooling by testing injection moulds and other tools before machining them, maximising production-floor efficiency
- Unleash the creativity of your designers and manufacturers with solutions that bring ideas to life, free from the usual time or financial constraints
- Customise repairs, restorations and accessories with 3D-printed materials